ABOUT US
As a specialist in Superalloys Machining, MILGRED is one of the leading companies to offer you a complete range of high-tech machining operations to enable to produce finished Blades & Vanes and other hot gas path related components. MILGRED has the most advanced technologies for machining full Blades & Vanes to the highest level of quality in accordance to your specifications for the satisfaction of yours customers. A highly qualified staff coordinated by a team of engineers contributes to the development and on-going research of new technological opportunities. The customer is supported by the team in all technical and quality aspects, granting the on-time delivery of an outstading product. Our quality system is approved by several gas turbine manufacturers and MILGRED is certified by Bureau Veritas for ISO 9001 version 2015 MILGRED can really become your prime partner in producing finished parts.
2003
Year Established
200+
Different Type Of Projects
10+
Number Of Customers
50+
Number Of Employees
SERVICES & CAPABILITIES
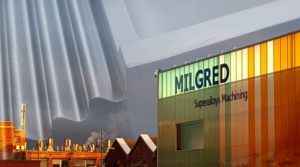
Engineering
We offer full engineering package, from qualification to mass production.
Our engineering team has extensive CAD/CAM skills as well as expertise in the process design and production management of the turbine hot-section parts. For further technical discussion please get in touch with the head of our engineering team.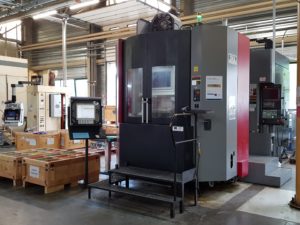
Machining & Fabrications
1) Creep Feed Grinding We are able to grind complete blades : Dovetail Tip radius Shanks Z form Sides
Our equipment : 4 creep feed grinding machines 2) 5 axis Milling Complete machining of turbine vanes. Our machines can accept parts with large dimensions. Our equipment : 3x 5 axis milling center with 2 pallets (MANDELLI – OKK). 1x 3 axis milling center with 1 large pallet (OKUMA). 3) TIG Welding We are able to perform the welding of Nickel / Cobalt-based superalloys parts such as hard-facing on « Z-notch « . Our equipment : TIG welding equipment 4) EDM (Electrical Discharge Machining) The core competence of the company is to realize following operations on parts : Drilling holes in inner and outer band & rows on vanes Faces Slots Our equipment : 7 EDM conventional machines (ONA/AGIE) + 1 WEDM machine 5) STEM (Shaped Tube Electro Machining) Our latest innovation to purpose the best high technology in terms of precision and quality. Specially used for increasing the turbulence of cooling air in turbine blades. Our equipment : 4 STEM Drilling Systems. 6) 5-Axis Fast Hole Drilling The best and fastest way to drill complex holes : a mix of diameters and at different angles. Our equipment : Two 5 Axis Fast Hole Drilling machines (MAKINO/BEAUMONT)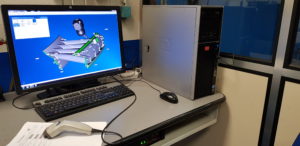
Tests & Qualifications
1) Ferric etching Acid attack before F.P.l, to clean parts.
Our equipment : Ferric etch line. 2) F.P.I (Fluorescent Penetrant Inspection) lnspection method used to detect cracks and discontinuities on parts after machining. Our equipment : F.P.I line 3) C.M.M. units (Co-ordinate Measuring Machines) A three dimensional measurement system to inspect parts with a complex geometry. Our equipment : 5 C.M.M. in air-conditionning. 4) Profile Projector To compare theoretical profile with achieved profile. Our equipment : 2 Profile Projectors, ‘1000mm in diameter each. 5) Ultrasonic testing With this method, we inspect the position of hole and control the wall thickness of the part. Our equipment : One ultrasonic depth test instrument. 6) Airflow testing We can measure air mass flow up to 0,66 lbm/sec using one of the three flow methodes : plenum pressure, pressure ratio or flow parameter, Our equipment : One airflow system (C.C.D.I.). 7) Moment weighting With this system, we can define the gravity center of the part. Our equipment : One moment weight system (SCHENCK). If required, other special tests such as X-Ray, metallurgical tests, etc, can all be arranged externally with specialized and approved laboratories, with whom the company has long established co-operation agreements.CONTACT
Head Office4 rue Jacqueline Auriol, 90000, Belfort, France
Tel : + 33 (0)3 84 21 95 90 E-mail : contact@milgred.com